Secondary battery
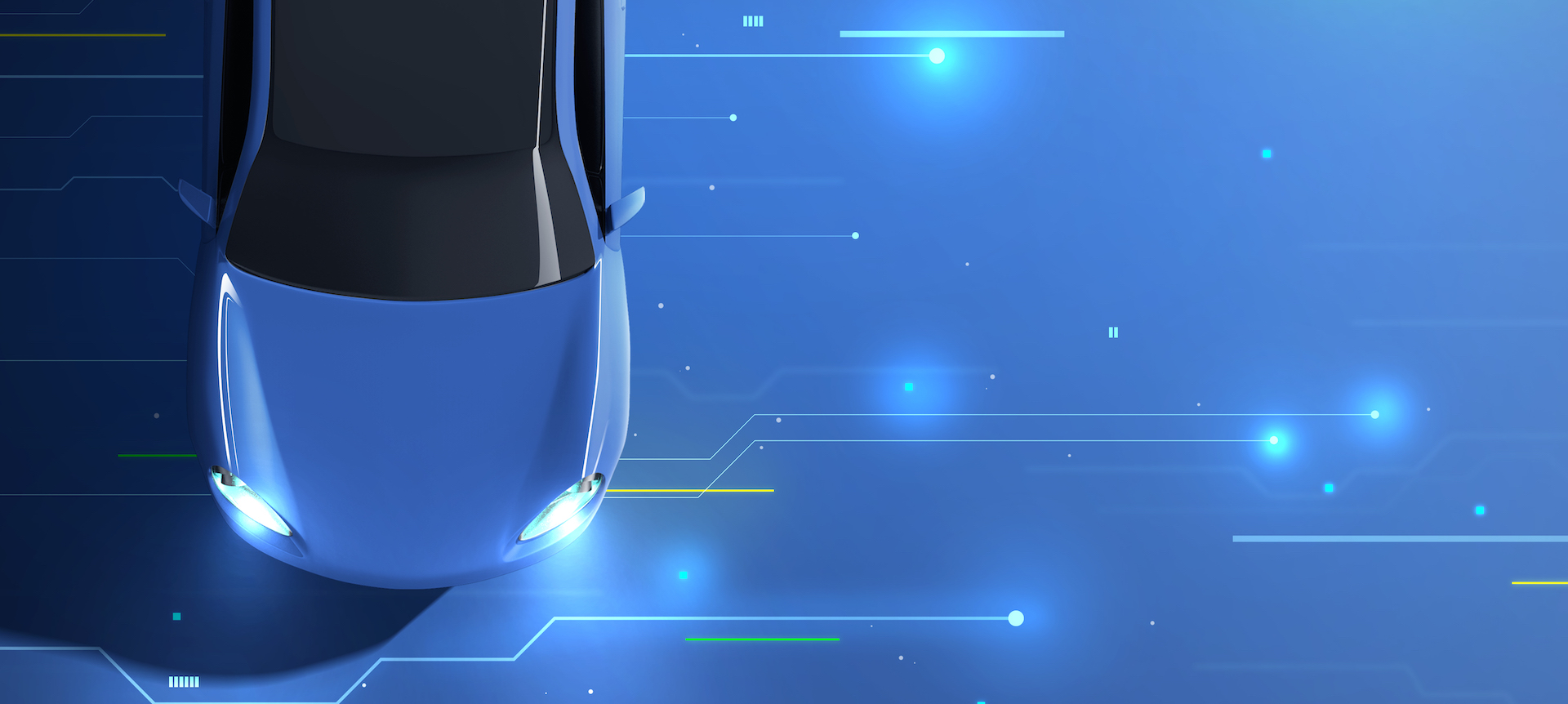
Capacity, condition measurement and inspection of the secondary battery
To be Updated
Measurement
Battery film thickness measurement
1. Measure the thickness of the aluminum (edge) layer of the pouch battery in a non-contact manner
It is necessary to measure the entire thickness of the film of the battery anode, cathode, and separator in the sealing part of the pouch-type battery housing for an electric vehicle produced in a roll-to-roll method in a non-contact manner. In this case, it may be adopted according to the specific material and characteristics of the film to be measured among confocal or interferometric technologies
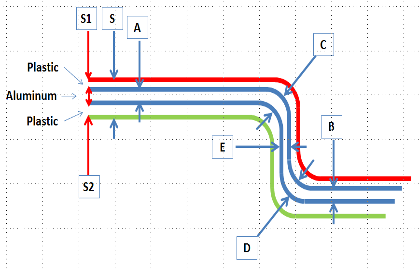
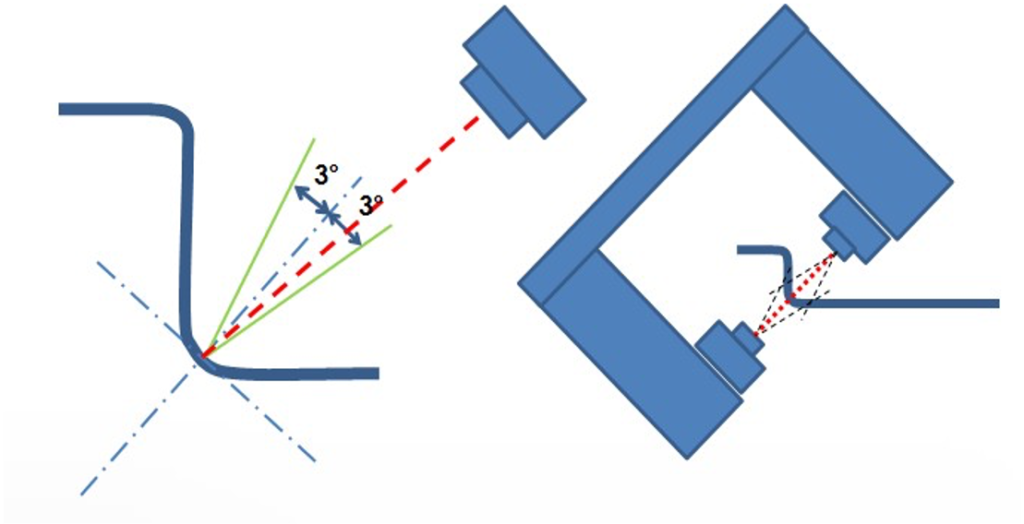
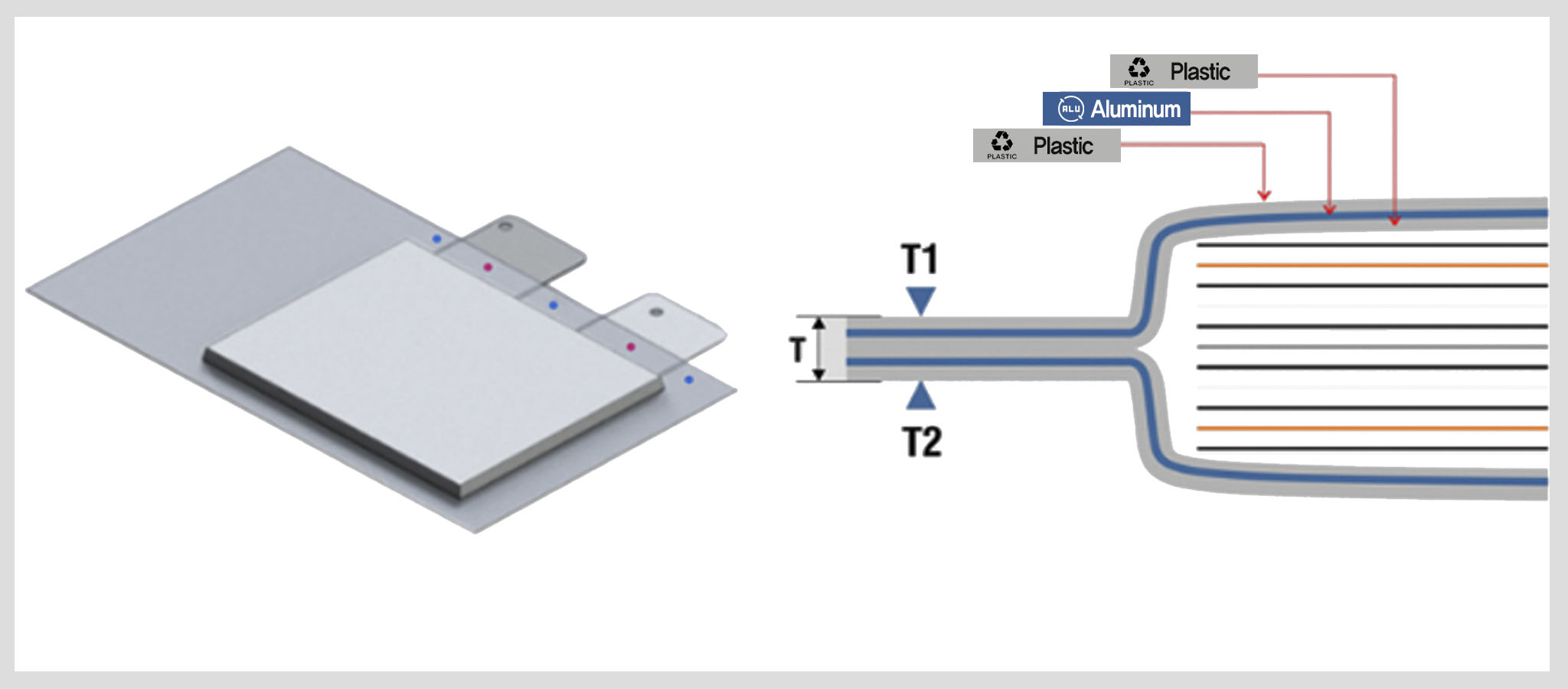
The overall thickness T shall be measured in a contactless manner at various locations in the sealing part of the pouch battery housing.
At this time, the measurement of the thickness T for each location is calculated by converting the sum of the measured values of the two non-contact transducers T1 and TZ.

MULTIPLE TECHNOLOGIES AVAILABLE TO MATCH ANY POSSIBLE REQUIREMENT AND TOLERANCE SPECIFICATION, UP TO MEASURING PERFORMANCE IN THE SUB-MICRON RANGE
3. Confocal Technology Solutions
In the case of a film made of a material similar to some plastic layers of the pouch battery cover foil that transmits white light, a confocal probe can measure the film thickness of individual layers. For a confocal sensor with a measurement range of 0.4 mm, a precision of about 0.055 µm is guaranteed, which can manage the strict thickness tolerance of the positive (+) film and the negative (-) film after calendering. Two probes are required to measure the overall thickness of the film.

Principle of Multicolor Confocal Measurement with Non-Contact Measurement Equipment using the confocal technology. As shown in the figure below, the battery pouch has several layers. The outer plastic layer may be covered with white light, and the inner aluminum layer may not be covered with white light. Therefore, there are two reflective ice sheets. The first is from the outer surface of the plastic to the sensor. The second is from the aluminum surface to the sensor. The two beams will have maximum intensity at two different wavelengths, which are common for the distance from the optical sensor to the two surfaces. To measure the distance, the two peaks should be separated sufficiently for easy identification and the peak length of the corresponding waveform should be high.
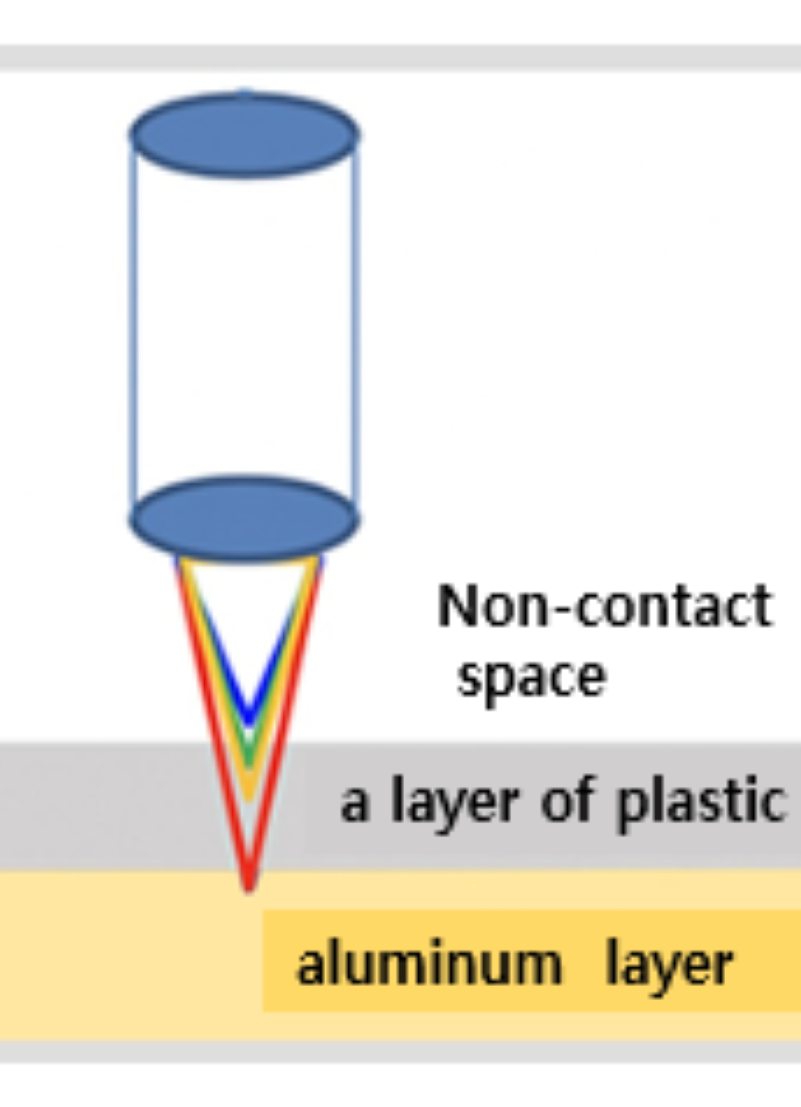
It is a non-contact sensor product based on chromatic aberration confocal technology capable of measuring the distance and thickness of all materials through which white light is transmitted. The thickness of up to five layers may be simultaneously measured, and the controller may be used with various optical probe families according to a measurement range, a sensor size, and a measurement specification that meets the requirements of various applications.
It is necessary to measure the width of the end of the film after the sitting process during the non-firing battery process produced in a roll to Rdll method. For this, a laser micro is used.
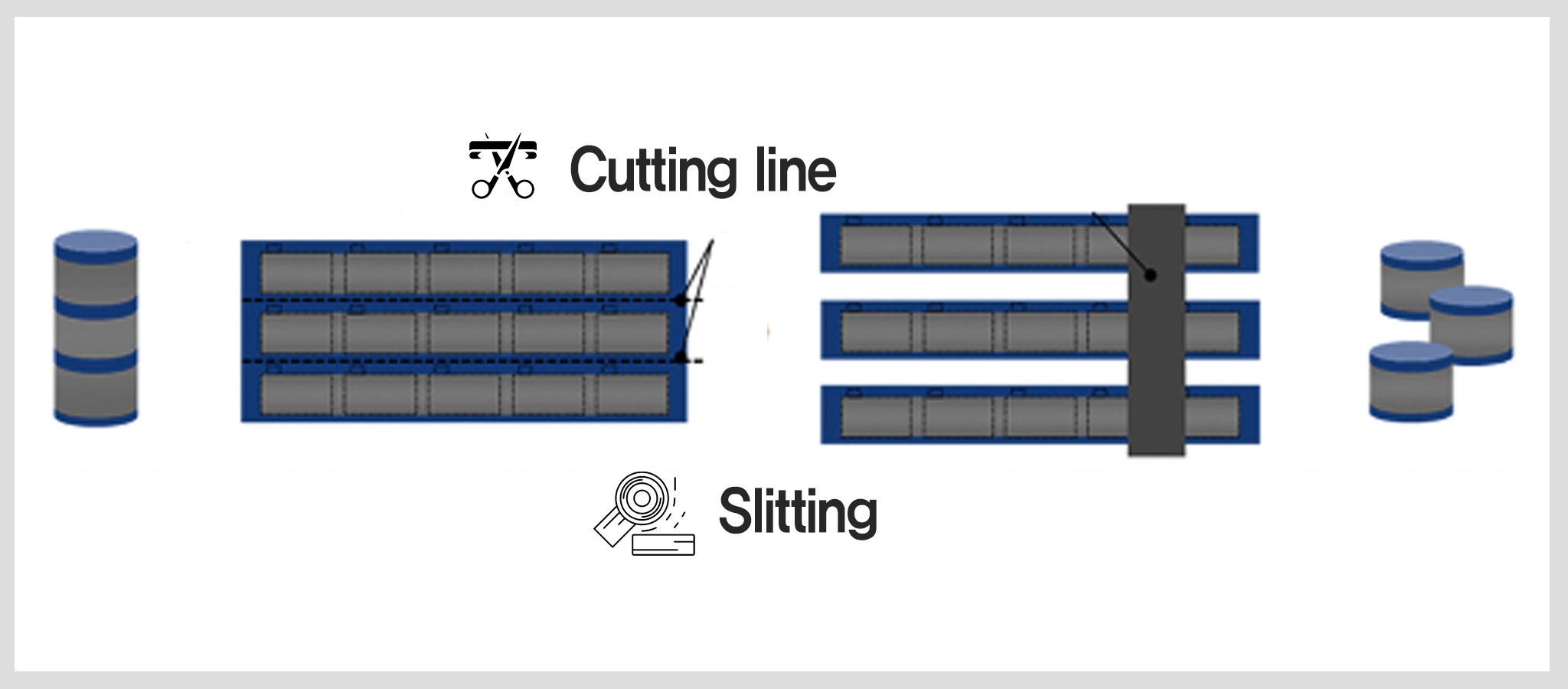
It is necessary to measure the width of the end of the film after the sliding process during the pouch-type battery process.
The Aeroel™ XLS150 laser oath can very accurately measure the width of the battery film up to 148 mm. In the case of a large piece of writing, two sensors can be used together. It is an intelligent sensor that can be directly connected to an electronic device without an external device, and is suitable for in-line applications.
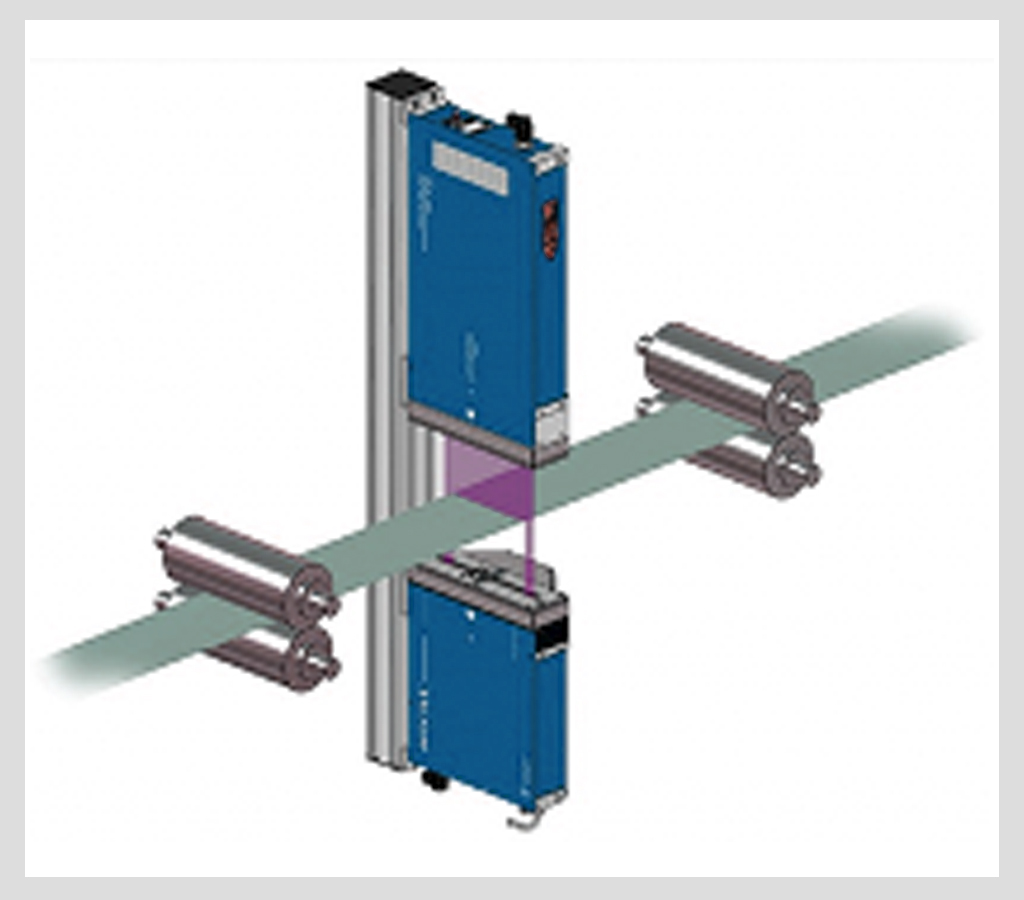
XLS150 Laser Sensor
Measurement
Roll to Roll XRF
■ Roll to Roll XRF
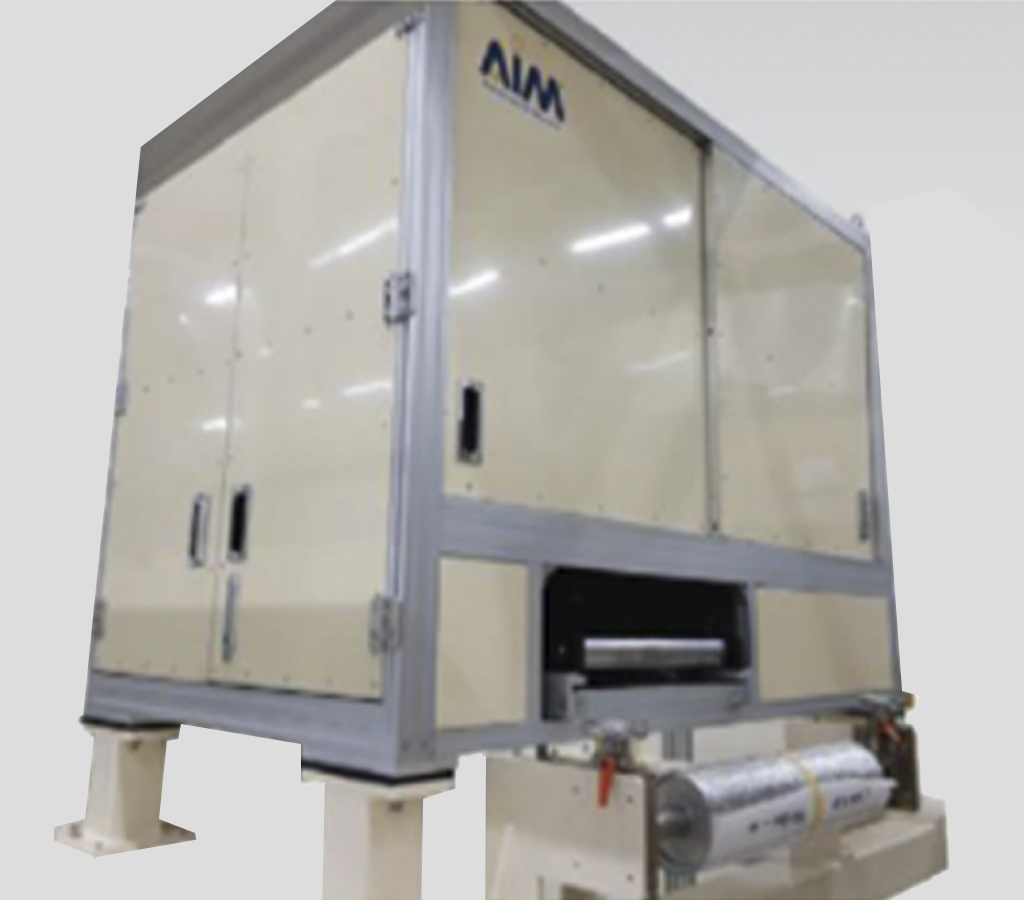
■ Product Features
The inspection equipment of the Roll to Roll XRF method includes secondary batteries, hydrogen cells, solar cells, etc
It is an equipment that inspects the thickness and content of the battery (Anode, Cathode).
In general, it is possible to check the thickness and content of various materials such as Pt, Co. Ni. CIGS, Cu. Zn, and Fe.
** The intensity of the X-ray is inversely proportional to the square of the distance.
It is built with a groundbreaking structure that minimizes the distance between the X-ray generator and the sample.
AIM XRF maximizes the intensity of X-rays by reducing the distance by two to three times compared to conventional measuring instruments.
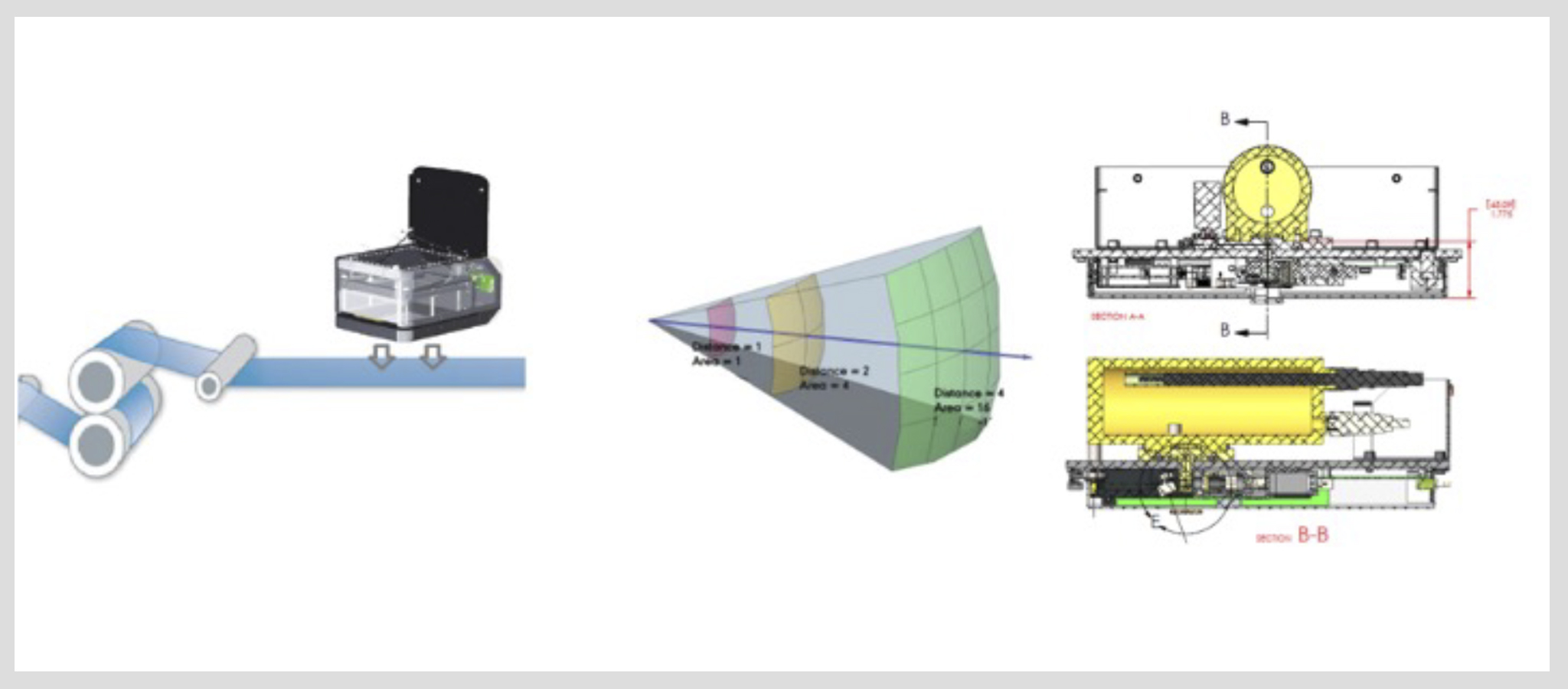
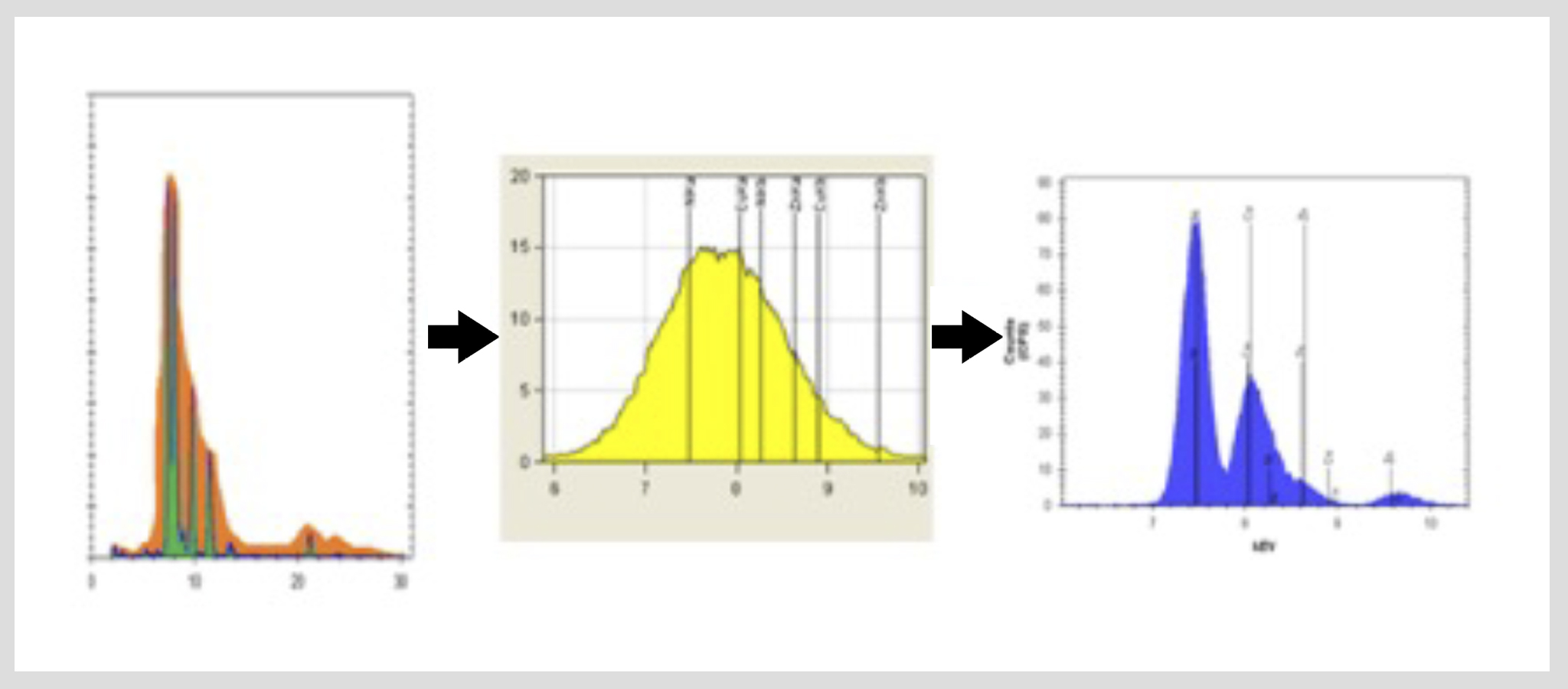
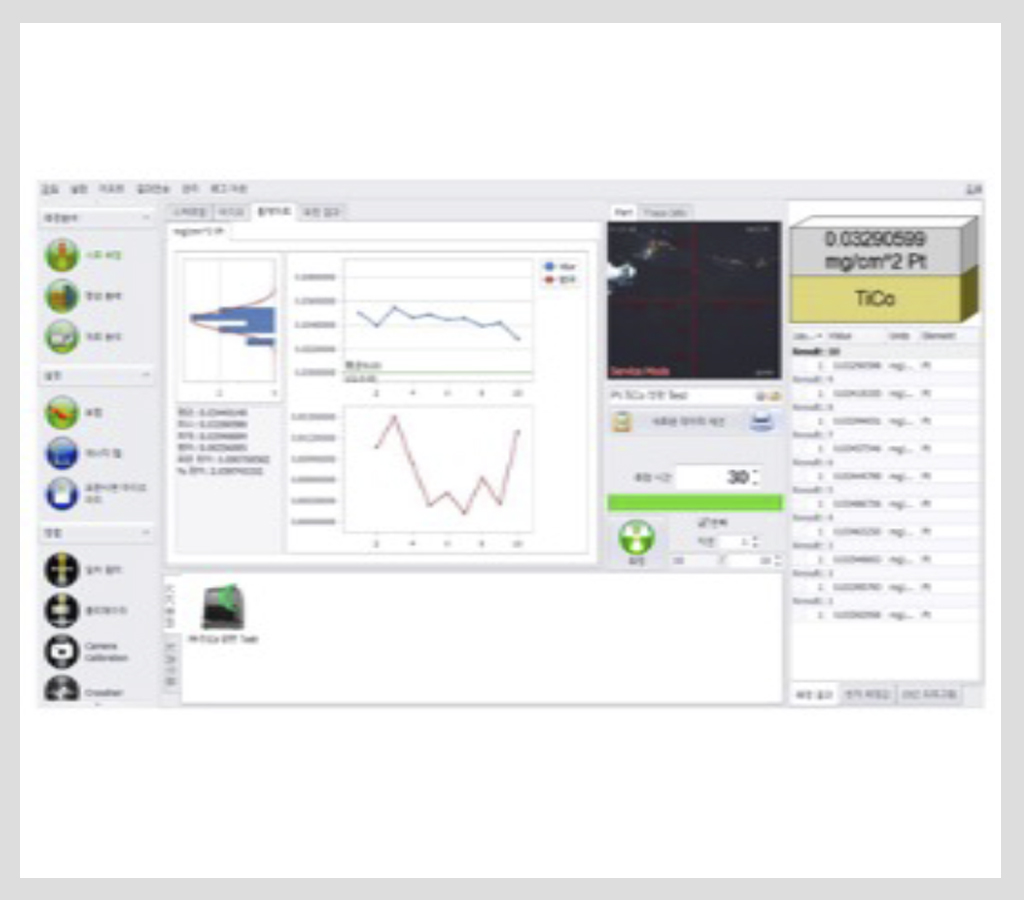
In - Line XRF
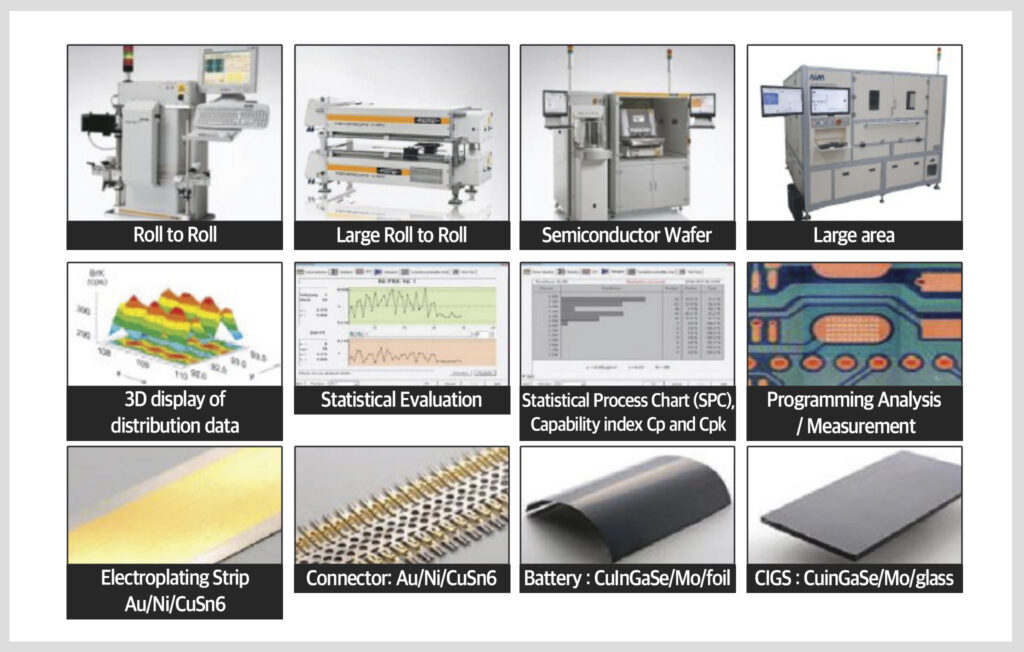
General Specifications
• Analysis possible elements: simultaneous analysis of 24 elements of AI(13) to U(92)
• Equipment Structure : Design equipment structure for measurement sample
• Positive (survey) direction: Top to bottom or bottom to top
A secondary battery, a hydrogen battery, a metal film, and a transparent film. Measurement of material composition ratio, plating thickness, and metal thin film
- measurable area

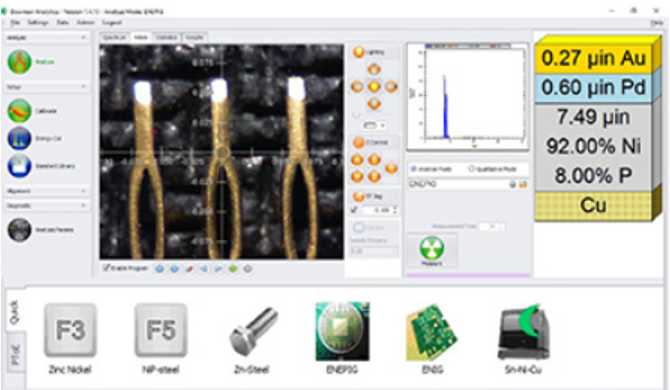
